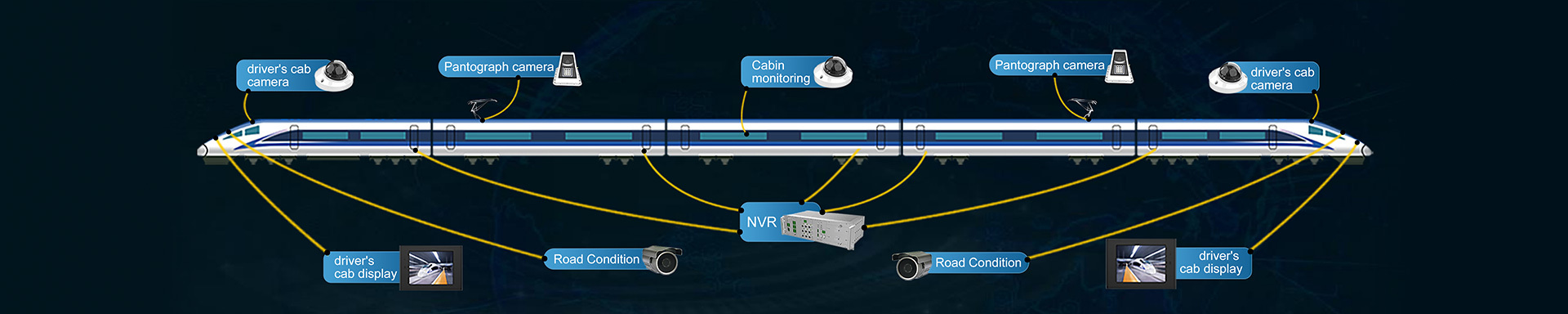
The cause of pantograph failure of rolling stock
2022-07-02 09:42Abstract: The pantograph is a piece of crucial traveling equipment for electrified railways. To ensure the safe and reliable operation of the contact network, we must improve the accuracy of the technical parameters of the pantograph maintenance in the process of contact network operation and maintenance and continuously improve the operation quality and safety reliability of the pantographs.
The cause of pantograph failure of rolling stock
Slat wear. The rapid wear of the slats is a normal phenomenon in the initial operation of the electrified section.
The root cause of excessive wear of the slider bar is:
① Mechanical wear. The bottom of the new line contact network profile is rounded, and there are many hard burrs on the surface of the contact line, which is the main reason for the rapid wear of the newly opened line slider strip. After many operations, the contact wire tends to be flat and smooth. The friction coefficient is reduced. After reaching a certain number of frictions, the mechanical wear will be significantly reduced and will remain within a specific range;
② Electrical abrasion. The new opening line contact wire leads to more burrs, and the surface is contaminated due to exposure to the air before opening. When the initial contact with the pantographed slide is poor, the electrical sparks are often large, and the electrical wear is naturally prominent.
The bow net pulls arc.
When the contact pressure is too small or even zero, the pantographed slide will break away from the contact network offline. Although a small or medium offline does not affect the operation of the locomotive, the sparks or arcs generated at the moment of offline will increase the electrical wear of the contact wires and pantograph sliding plates, shortening their service life. A large offline is very harmful and even threatens the operation and safety of the locomotive. Therefore, offline should be avoided as much as possible, whether from extending the life of contact wires and pantograph sliding plates or from the standpoint of locomotive operation safety.
The pantographs themselves are addressed in the following ways for the offline problem.
① Improve the pressure between the pantographed slide and the contact wire. Contact pressure is related to contact network structure, line condition, and locomotive running speed. Testing under the original electrified line and locomotive running speed determine the current pantograph contact pressure.
② The friction at each articulation of the pantograph plays a role in reducing the contact pressure when the bowed head moves upward and should ensure that the movable joints are well oiled and move freely. Ensure that the spring of the bracket is not broken, the elasticity is appropriate, and the slide plate is flexible in rotation.
Pantograph parts are damaged.
When the locomotive runs at high speed, the pantographs are subjected to complex forces. The harsh working environment makes the pantograph parts prone to various problems, which will cause hidden dangers if not found and handled in time. Damage to components is mainly concentrated in the salmon acid seat, triangular plate, bottom frame, upper frame, and abduction arm. This requires that when inspecting the pantographs in the depot, the parts mentioned above should be checked, and those that do not meet the technical requirements should be dealt with on time to avoid bringing hidden problems to the line.
In summary, The leading cause of damage to the pantograph is the wear and tear contact of the ascending and descending bows and the pantograph mass, and the actual cause must be found to protect them. To eliminate all accidents, you must never mount the car's roof when the pantograph is not disconnected from the contact network or before confirming that it is not energized. Check that the pantograph has been stabilized on its two underframe rubber stops before climbing on the vehicle. Before performing any inspection, lubrication, adjustment, or overhaul work, the vehicle must be operated in a power-free zone (no contact network) with the small spool hooked to the bottom bracket.